Potatoes are treated using Pulsed Electric Field (PEF) system (Elea GmbH) in an industrial setting.
Pulsed Electric Field in Potato Processing: Impact on Sustainability
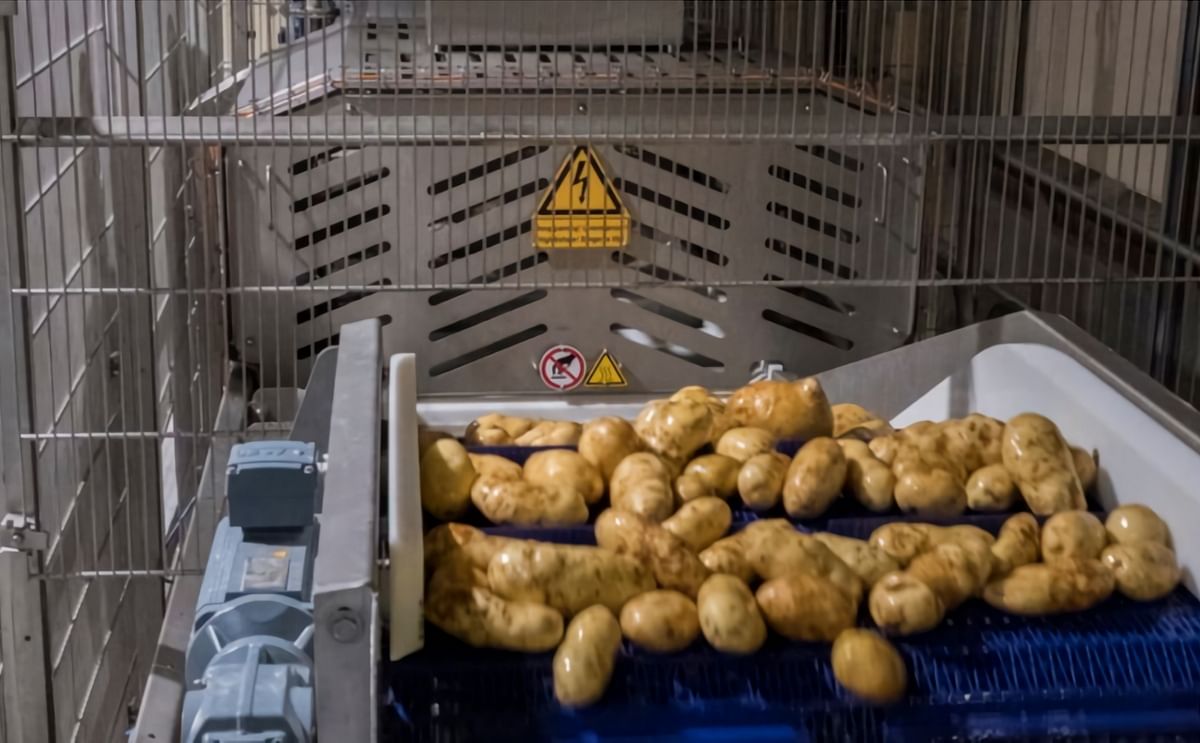
A study on the impact of Pulsed Electric Field treatment (PEF) in the potato processing industry has shown substantial benefits in comparison to the regular process using conventional pre-heaters.
In particular the effect on the environmental impact / sustainability of the process is substantial. The study was recently published online and is due to be published in the October issue of the Journal of Food Engineering.
Reference
Fauster, T., Schlossnikl, D., Rath, F., Ostermeier, R., Teufel, F., Toepfl, S., Jaeger, H. (2018) Impact of pulsed electric field (PEF) pretreatment on process performance of industrial French fries production. Journal of Food Engineering 235:16-22. https://doi.org/10.1016/j.jfoodeng.2018.04.023(Full access requires subscription)
Life Cycle Analysis (LCA) allows characterizing environmental impact of production from cradle-to-gate.
A study on the application of Pulsed Electric Field treatment in the potato processing industry has been conducted in an industrial scale using benchmarking data of Elea clients worldwide.
The study has shown, that by replacing conventional preheaters with PEF equipment, the energy requirements can be reduced by 85 % and water consumption can be reduced by 90 %.
In addition, a reduced fat uptake, an improved product quality and a 1 to 1.5 % increase of product yield have been observed.
For a 50 ton/h french fry line that corresponds to 60 – 70.000m3 of water and 20 GJ of thermal energy savings per year.
This is in line with earlier results (McHugh, T. and Toepfl, S. (2016) Pulsed Electric Field Processing for Fruits and Vegetables. Food Technology 70:1 73-75 ; access requires subscription)
Similar results have been published in sustainability reports of two major PEF users Simplot and Lamb Weston.
In the scope of cradle-to-gate, it results in around 20-30% overall reduction of environmental impact.
PEF at Lamb Weston / Meijer (2016)
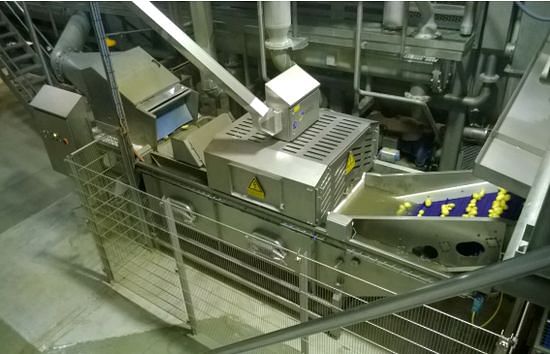
Pulsed Electric Field application
The implementation of PEF has enabled us to save eight percent of our fresh water usage, or 70 million litres per year, in our Bergen op Zoom plant.
It has also enabled us to reduce our energy use by five percent per year, and improve our frozen product recovery.
Source: Sustainability Report 2015-2016 Lamb Weston / Meijer (water)
PEF at Simplot (2014)
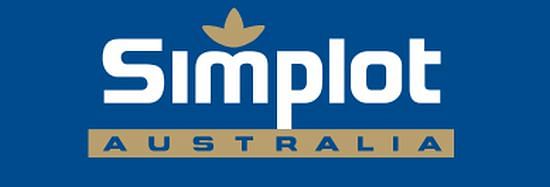
We have invested in new technology to help improve the quality and efficiency of our potato manufacturing process. The conventional method of potato cutting involves a step where potatoes may be submerged in hot water in excess of 50 degrees for more than 40 minutes.
While this assists in improving cutting yield and quality it can sometimes lead to a negative impact on the texture of the product. Our R & D team identified an opportunity to alleviate this issue and at the same time reduce energy and water costs by replacing the pre-heating step with pulse electric field technology.
This new technology works by applying electric fields into a water medium that transfers through the potato and has a softening effect. It is an instantaneous process that requires no heat and very little water and provides a better cutting quality with higher yield and no negative impact on texture.
Working in collaboration with the developers of this technology Simplot invested in laboratory and factory evaluations that resulted in the adoption of this technology not only by our Australian factories but also at a global level. Simplot is one of the first potato processing companies in the world to adopt this technology which has saved us on a global level in excess of 300,000 KL of water and 100,000 GJ of energy.
Source: Simplot Australia's Sustainability Report 2014