This could have been the last year for the Malin Potato Co-op. Instead, the 52-year-old company is building a state-of-the-art, $7 million potato packing facility to move it into the future of agriculture.
“It’s exciting,” said Dave Cacka, general manager for Malin Potato Co-op. “We’re looking forward to getting this operational. The fellas that own the co-op, they’re doing this for the future of ag in the Klamath Basin. It’s for the young guys coming up. If we can find a niche that works, and they can make a profit, that’s the thing to do here.”
The new building is nearly done. Cacka hopes it will start packaging potatoes later next month.
The building is 40,000 square feet and houses equipment from New Zealand, Slovakia, Canada, and from the old shed across the railroad tracks in Merrill.
“It’s an international effort,” Cacka said. “It’s light years ahead.”
The history
Malin Potato Co-op was approached about the idea of building a new shed in November 2013.
At the time, things weren’t looking good for the company.
“With the way potato acreage has been going in the Basin, they’re growing less and less acres and less and less acres,” Cacka said. “This probably would have been the last year for the Malin Potato Co-op.”
Also the old packing facility was out of date, an aging wooden structure built in the 1930s and ’40s and added on to over the years.
“The equipment is antique; they don’t make it any more,” Cacka said.
But as the board was considering its demise, a group of organic potato farmers stepped up saying they wanted a state-of-the-art packing facility.
“They decided to do it. Take the risk,” Cacka said. “It’s a big risk.”
The now
The co-op found financing help from Washington Federal on the big, $7 million project.
It hired Volm Companies, of Wisconsin, to design the facility.
Workers from Wyma, of New Zealand, built and installed the potato washing and polishing machines.
The conveyors, holders and holding tanks came from Canada, and the packaging machines came from Holland.
Talking really state-of-the-art, an Odenberg machine is an optical sorter, which reads each potato with a computer and decides if that potato is the right size, shape and quality to be packaged.
“It will look at the potatoes with the optics, and you can pre-program it to grade your potatoes,” Cacka said. “It’ll look at all kinds. It’s computerized. Just program it for whatever variety.”
The Odenberg was built by an Irish company in Slovakia.
On Wednesday, workers were installing a sizer, which puts potatoes in cartons and boxes. That particular machine moved from the old shed to the new.
“That’s the only piece of old equipment,” Cacka said. “We saved $850,000 by using that. It’s a good machine.”
Malin Potato Co-op has been certified to package organic potatoes for years, Cacka said. The new facility will be able to package both organic and conventional potatoes.
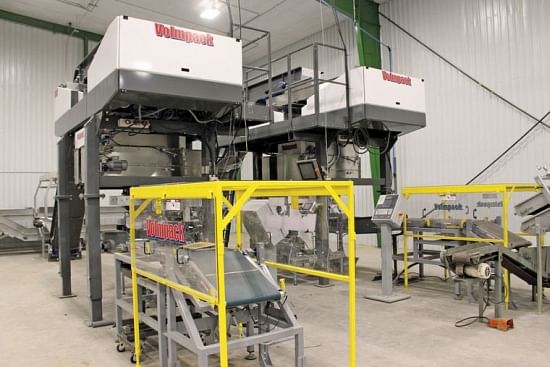
These Volmpack baggers can package potatoes in bags ranging from one pound to 20 pounds. They are one of many new pieces of equipment in the Malin Potato Co-op packing shed being built in Merrill.
The future
All this new equipment and automatizing means Malin Potato Co-op will hire fewer seasonal laborers for its packing operations. But it also will mean better efficiency and moving more product through the shed.
The optical sorter is a prime example.
Before, workers would sort the potatoes by hand. They would look for defects and cull out any potatoes not good enough for packaging.
“When you’re talking red and yellow organic potatoes, you get into lots where you’d cull 70 percent of them out,” Cacka said.
To do that by hand, everything slowed down, increasing hourly costs.
“With the new optical sorter, 80 percent of that will be done with automation,” Cacka said. “We’ll be able to run more sacks per hour. Those costs will go down.”
Speaking from his experience, Cacka thought this facility might be the first new potato packaging shed built from scratch in Oregon for 30 years. Companies often upgrade old facilities but rarely build new, he said.
“If you compare it to packaging sheds in Idaho, in Washington — it’s small,” he said. “But if you compare it to packing sheds in Oregon, in the Klamath Basin — it’s big.”