Innovative Palletizing Efficiency: Scott's Hybrid Solution Unveiled
Innovative Palletizing Efficiency: Scott's Hybrid Solution Unveiled
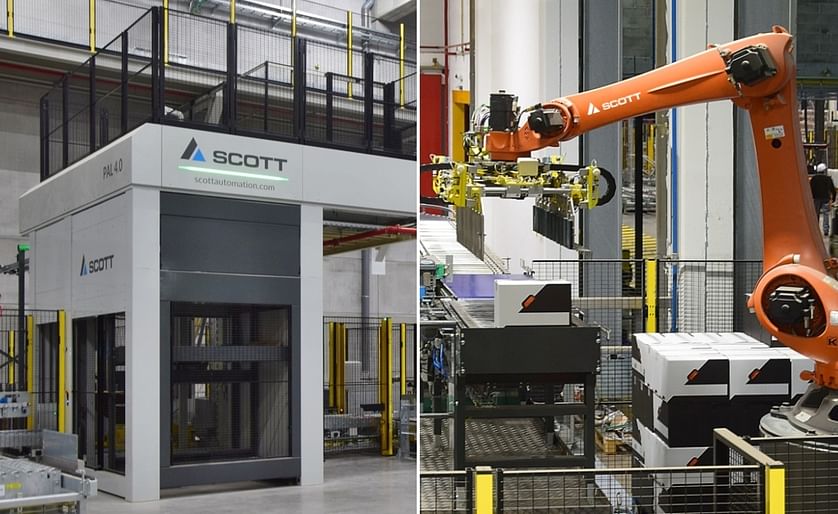
Palletizing, the process of stacking products on a pallet for transport and storage, is a critical aspect of manufacturing and distribution. The efficiency, reliability, and flexibility of the palletizing system can significantly impact operational productivity.
Traditionally, this process has been categorized into three types: manual, conventional (layer), and robotic palletizing. Each method has distinct characteristics and benefits suited to different operational needs. For brevity, this paper will omit manual palletizing.
Conventional Palletizing
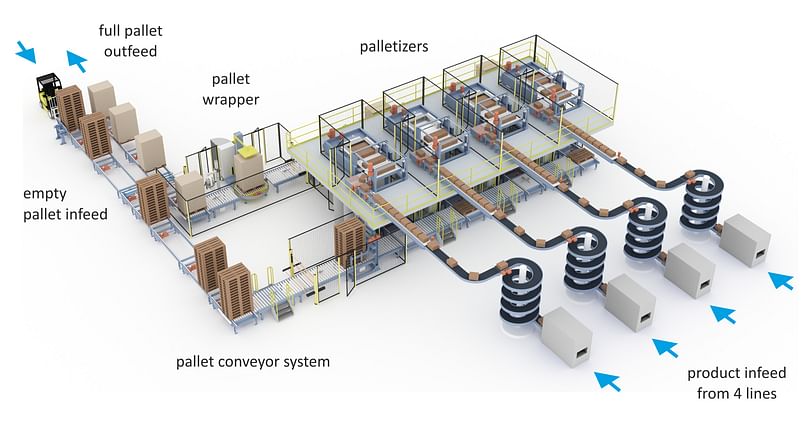
Conventional Palletizing
Conventional palletizing systems, also known as layer palletizers, stack products in a predetermined sequence, creating stable and uniform layers on a pallet. Product is brought into the machine on an infeed conveyor, cases are turned to form specific patterns, and then the row is raked onto an apron. Once a full layer is formed, the apron moves away to deposit the layer on the pallet.
Benefits:
- Higher Production Rates: Conventional palletizers are renowned for their speed and efficiency. They are capable of handling high-volume product flows (upwards of 200 cases per minute), making them ideal for high-capacity operations.
- Handling Multiple Case Sizes and Types: Because the bottom is conveyed across rollers or a mat top, the palletizer may only require minimal adjustments if any at all. These systems can easily adapt to different case sizes and types, allowing for a versatile palletizing process suited for varied product lines. Most new systems have added automatic adjustments to eliminate the need for change-over time.
- Simple Operation and Maintenance: The mechanical simplicity of conventional palletizers makes them relatively easy to operate and maintain, requiring less specialized personnel training. Conventional palletizers typically incorporate industry-standard PLCs and HMIs to make things easier on the operator.
Robotic Palletizing
Robotic palletizing involves the use of robotic arms, equipped with various end-of-arm tools, to pick and place products on a pallet. End-of-arm tools may be custom designed specifically for a customer’s product. This method offers greater precision as well as label orientation during placement.
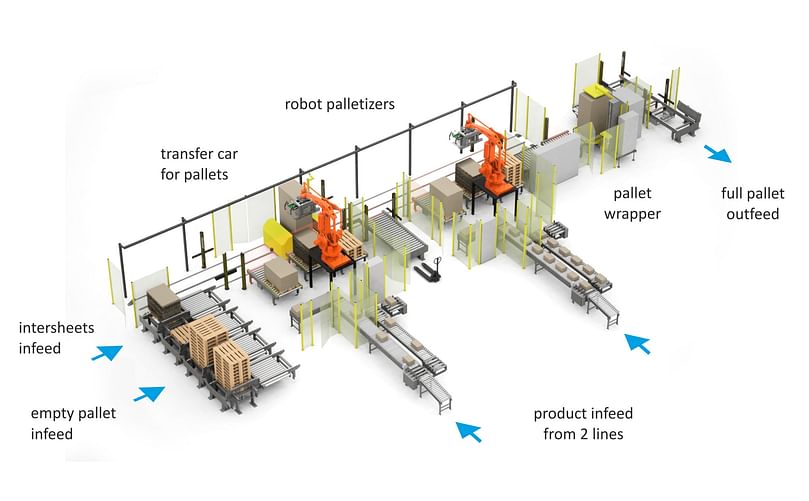
Robotic Palletizing
- Simultaneous Multi-Line Palletizing: Robotic palletizers can build different product loads simultaneously, making them ideal for operations that require palletizing a variety of items concurrently.
- Label Orientation Control: These systems can orient products based on label positioning, ensuring that labels are visible and correctly aligned, which is crucial for retail and customer-facing products. Vision systems may be added to further improve accuracy.
- Adjustable Infeed Elevations: Robotic palletizers offer flexibility in infeed elevation, accommodating different product lines and operational layouts without extensive mechanical restructuring. Pick-up points do not need to all be at the same location so long as they are within the arms operating reach.
Comparison and Considerations
When choosing between conventional and robotic palletizing, factors such as product type, production volume, space, and workforce must be considered. Conventional palletizers are best suited for high-speed, uniform product lines, while robotic palletizers excel in environments requiring flexibility and precision handling.
Scott's Innovative Solution: A Hybrid Approach
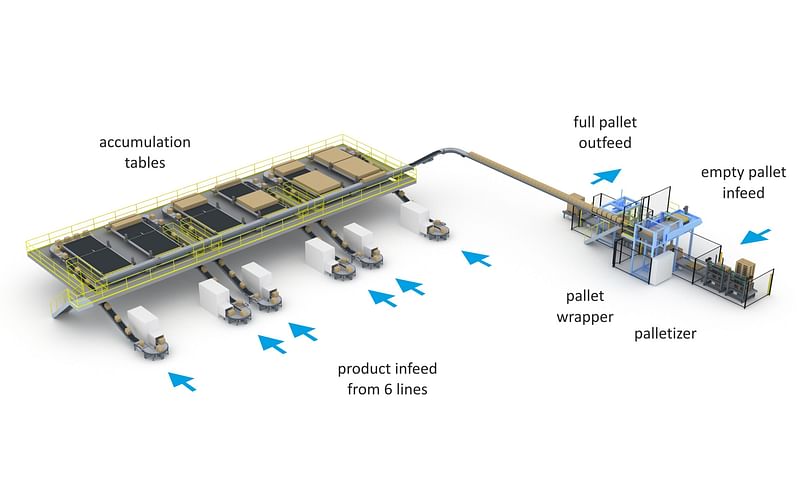
Scott's Innovative Solution: A Hybrid Approach
Scott presents an innovative solution that bridges the gap between conventional and robotic palletizing. Scott's advanced accumulation tables allow customers to enjoy the benefits of both systems by storing at least a full pallet worth of product before sending it to the palletizer. Depending on the customer’s overall production rate, up to ten tables could feed a single palletizer.
Palletizing Process
Key Features:
- High-Capacity Palletizing: Like conventional systems, Scott's solution supports high-capacity palletizing, ensuring productivity in high-volume scenarios. Multiple palletizing options provide capacities from 20 cases per minute up to 150 cases per minute.
- Multi-Line Capacity: Incorporating the storage capacity in the accumulation tables, it can handle multiple product lines simultaneously, a feature typically associated with robotic palletizers. Whereas a robotic palletizer may be at the limits with a total production rate of 20-30 cases per minute, accumulation tables allow four or five lines EACH running 20-30 cases per minute to feed a single palletizer.
- Integrated System Design: This solution provides an integrated approach, combining the efficiency of conventional palletizing with the adaptability of a multiline system.
Conclusion
The choice between conventional and robotic palletizing depends on specific operational needs. However, Scott's innovative accumulation tables offer a hybrid solution, merging the high-capacity capabilities of conventional systems with the flexibility and precision of robotic palletizing. This integrated approach represents a significant advancement in palletizing technology, offering businesses a versatile and efficient solution to meet diverse and evolving palletizing demands.