Simplot's 4Sight 2030 Goals
Simplot's 4Sight 2030 Goals
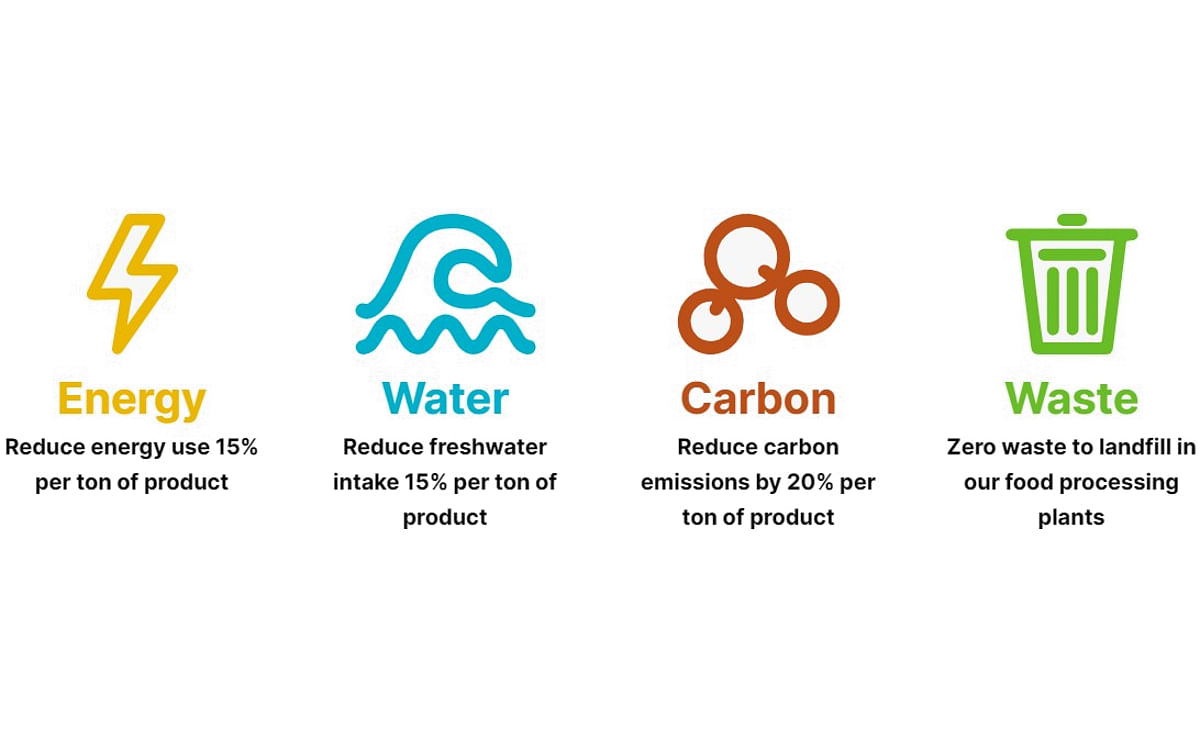
Recently Simplot, a potato processor and a supplier of a wide range of agricultural products, highlighted its sustainability goals.
Since Simplot covers all aspects of the agricultural value chain, the company can tackle agricultural sustainability issues like nobody else, and that’s the approach they’re taking with their new sustainability goals.

They've done a lot to reduce energy consumption in the past 10 years, but they can dig deeper. This next phase asks them to go beyond the obvious and into true innovation and true leadership. Their 4Sight 2030 goal for energy is to reduce energy use 15% per ton of product by 2030. With the help of their employees and all Simplot locations, this is a goal they know can be reached.
The J.R. Simplot Company has specific and measurable sustainability goals. These operational goals are aimed at major reductions in energy, water, carbon and waste emissions by 2030.
Having a dedicated plan enables them to more accurately map their future and track their progress, both globally and within every country in which they operate.
Energy
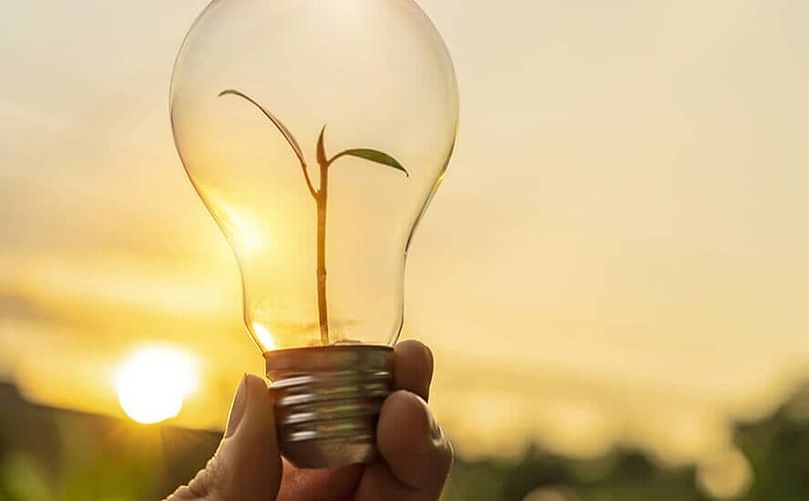
Energy
Power Their Production Sites with Renewable Energy
Simplot scientists and engineers are using anaerobic digesters to convert waste into gas that can be used to reduce their waste and energy consumption. Anaerobic digestion uses bacteria to consume the waste products and create methane, a core component of natural gas and other fuels.
Recover Heat, Convert It to Renewable Energy
Simplot's Ulverstone site in Tasmania, Australia installed a 500-kW heat exchanger in 2018 that recovers heat from the refrigeration system and uses it to pre-heat boiler feedwater. This system makes use of recovered heat that previously would have been vented to the atmosphere, but now saves them about 16,000 gigajoules of natural gas per year.
Similar principles are applied at their fertilizer manufacturing sites, as they reduce energy consumption through heat recovery. The heat generated by chemical reactions at their facilities is captured and used as an energy source.
Achieve and Sustain ENERGY STAR Excellence in Food Processing and Manufacturing
Simplot is an Energy Star Industrial Partner. All Simplot food processing plants in the U.S. and Canada have earned Energy Star Certification, an annual award given to facilities that perform in the top 25% for energy efficiency among similar facilities in its industry.
Their Portage La Prairie facility in Canada has met the energy criteria for 10 consecutive years, officially earning Energy Star recognition in 2019 when the program extended into Canada.
In 2019, Simplot’s Helm plant in California became one of the first nitrous fertilizer plants to receive Energy Star certification. This pioneering accomplishment was repeated in 2020, when the Helm plant was certified for a second consecutive year.
Water
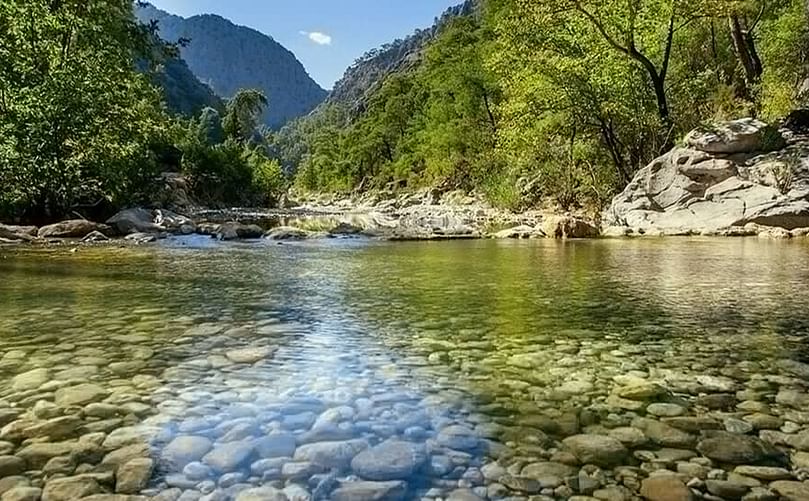
Water
Precipitation infiltrating through overburden disposal areas (ODAs) constructed by historical mining in the 1980’s and 90’s at the Smoky Canyon Mine has mobilized selenium into the groundwater. Groundwater discharge at Hoopes Spring and South Fork Sage Creek Springs contribute selenium to downgradient streams.
Simplot constructed a pilot water treatment plant (WTP) utilizing both physical and biological technologies to treat the impacted spring water. This unique and innovative treatment process uses two technologies.
Ultra-filtration (UF)/reverse osmosis(RO) membranes concentrate the selenium from the water; then a fluidized bed bioreactor (FBR) use specialized bacteria to reduce and precipitate selenium from water.
The selenium is then removed as a solid. Simplot’s water treatment plant began operating at a 1,700 to 2,000 gallon per minute rate in December 2017. The treatment facility removes approximately 80-90% of the selenium from a portion of the spring water.
Reclaim and Recycle Water for a 50% Conservation Rate
Simplot’s state-of-the-art, LEED Gold Certified potato processing plant in Caldwell, Idaho, saves energy and water while increasing production. Among its many innovations, the plant utilizes a reverse osmosis water filtration system that can filter and recycle up to 1 million gallons per day.
This reduces the fresh water use by nearly 50%, saving about 30 million gallons of water per month, with much of the remaining, nutrient-rich water applied to surrounding crops.
Carbon
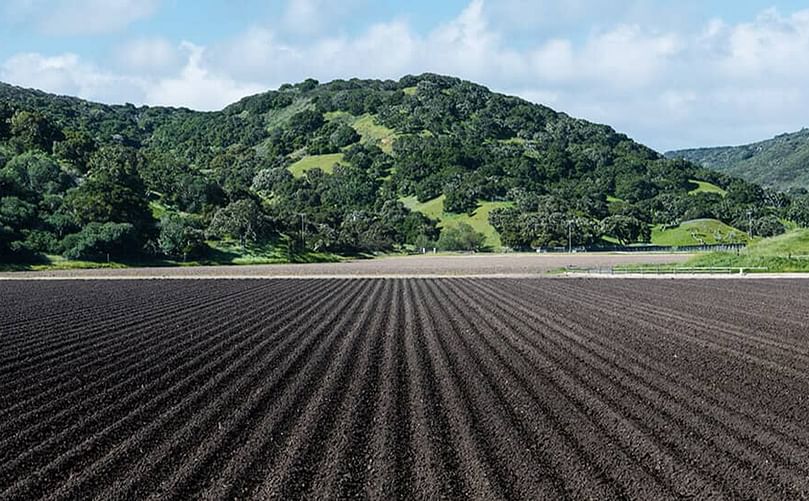
Carbon
Adopt Next-Generation Technology for Freezer Storage
Simplot recently invested in a new high-bay freezer for improved energy efficiency at their Caldwell, Idaho, plant. The building design minimizes energy loss and allows for a smaller refrigeration system that uses less energy but still maintains the freezer at -5°F.
The freezer also enabled Simplot to consolidate a variety of storage locations on site, helping reduce their transportation footprint and greenhouse gas emissions from trucking.
The project also included efficient lighting, heat pumps and reflective roof coating. In total, these improvements will save over 6.5 million kilowatt-hours of energy per year – enough to power more than 545 average-sized homes for one year. Two of their other potato production facilities employ similar new high-bay freezers.
Put Sustainable Fuels to Work for Potato Processing
Simplot has several projects in the works that use sustainable fuels. For example, Simplot’s Moses Lake Plant features a state-of-the-art boiler designed to burn three different fuels: natural gas, hydrogen and biogas. Hydrogen burns clean and has zero carbon emissions from combustion.
Simplot also has several operations across the country that capture biogas from anaerobic digesters. Biogas is a renewable resource generated onsite from the anaerobic digestion of potato waste that can be used as a sustainable fuel, allowing Simplot to eliminate waste and reduce energy consumption.
By combusting biogas and hydrogen, the site reduces its carbon footprint and natural resource consumption compared to burning only natural gas.
Waste

Food Waste
Cultivate Composting
After a successful six-month composting pilot program, Simplot constructed a new advanced composting facility in Portage La Prairie, Canada. The plant was designed to compost a variety of processing waste including wet waste, cull potatoes and soil residue.
As of 2020, the plant has composted 51,384 tons of waste, and is able to compost materials that would otherwise have been sent to landfills.
Its closed-loop design allows the facility to limit any nutrient-rich leachate run-off into the environment by capturing it in holding cells and reduces greenhouse gas emissions. The run-off is re-incorporated into the composting process to maintain optimal moisture levels within the compost windrows.
Reduce Food Waste
Simplot remains active in finding new solutions for reducing waste. This includes removing nutrient rich food solids from potatoes and repurposing it for food ingredients or cattle feed. We also repurpose another waste product, activated biosolids, to enrich livestock feed and as a soil amendment.