On 10 and 11 May, processing equipment manufacturer Tummers Methodic from Hoogerheide successfully organised two open days. Hundreds of specialists from the food processing industry at home and abroad marvelled at the largest Hex Polisher in the world and the very latest designs in clay and salt bath techniques. Tummers Methodic also received many enthusiastic responses in relation to the innovative, complete washing line that had been constructed in all its glory.
In fact, Tummers Methodic had already been made aware of interest in the washing line long before the actual open days. The eye-catcher had actually been constructed to be transported to a very enthusiastic client;the Danish potato company Thorsens Chipskartofler. This washing line is special as a result of several innovative techniques that have been specifically developed for this Danish client. The new clay bath product separator is a good example of this innovation.
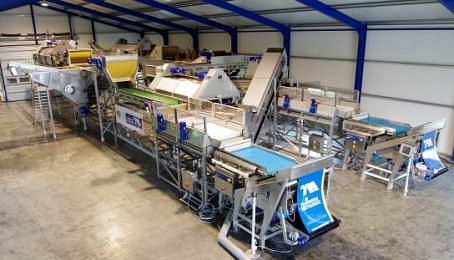
The complete and innovative Tummers Methodic washing line that was ready to be shipped to the Danish potato company Torsens was the subject of many enthusiastic reactions.
The machine is therefore more effective at separating desirable and undesirable potatoes and organic components. Separate water movement means that waxy potatoes and organic elements are eliminated from the product flow quicker and more effectively. The Danish company Thorsens Chipskartofler supplies the potatoes directly to the crisps industry. It is therefore vital that they ensure that no waxy potatoes end up in the final batch.

The newly developed product separator KB-450 encompasses a very clever design which means that its effectiveness is significantly increased.
Given the high capacity requirements of Thorsens Chipskartofler, Tummers Methodic has also developed a new type of Drum Polisher TP-1650x3750T for the potato company. This polishing machine has an impressive drum length of 3.75 metres and a diameter of 1.65 metres. The cleaning capacity amounts to as much as 35 tons of potatoes per hour. Never before in the world has such a huge hexagonal drum washer with washing brushes been used in a practical installation.
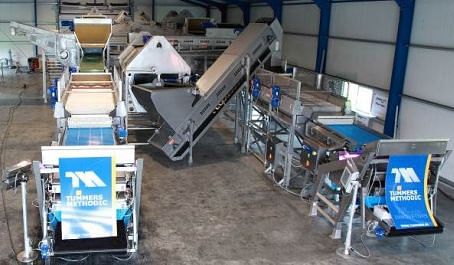
Worlds largest hexagonal drum washer is in the centre of the line. It functions as a bypass in case the potatoes need to be extra clean.
Tummers Methodic has been entrusted with the development of innovative machines for the past 35 years. Founder Fons Tummers always applied the motto ‘don’t complain, just get on with it’.
This mentality, coupled with genuine craftsmanship, has enabled the company to expand into a food processing company that is now active throughout the world. His son Erwin Tummers, who now heads up the business, aims to expand even further with the help of his hundred or so employees. He has therefore decided that Tummers Methodic should specialise in particular product groups. An example of this is the TM-knife blocks that the company developed and manufactures in-house.
All of these developments are exhibited by the manufacturer in their new office, reception and meeting rooms. As a result, Tummers Methodic will continue to provide pleasant surprises for its clients over the coming years.