Grisnich receiving, cleaning and sorting plant in China
Tolsma-Grisnich supplies potato receiving, cleaning and sorting section for french fries and potato specialty plant in China
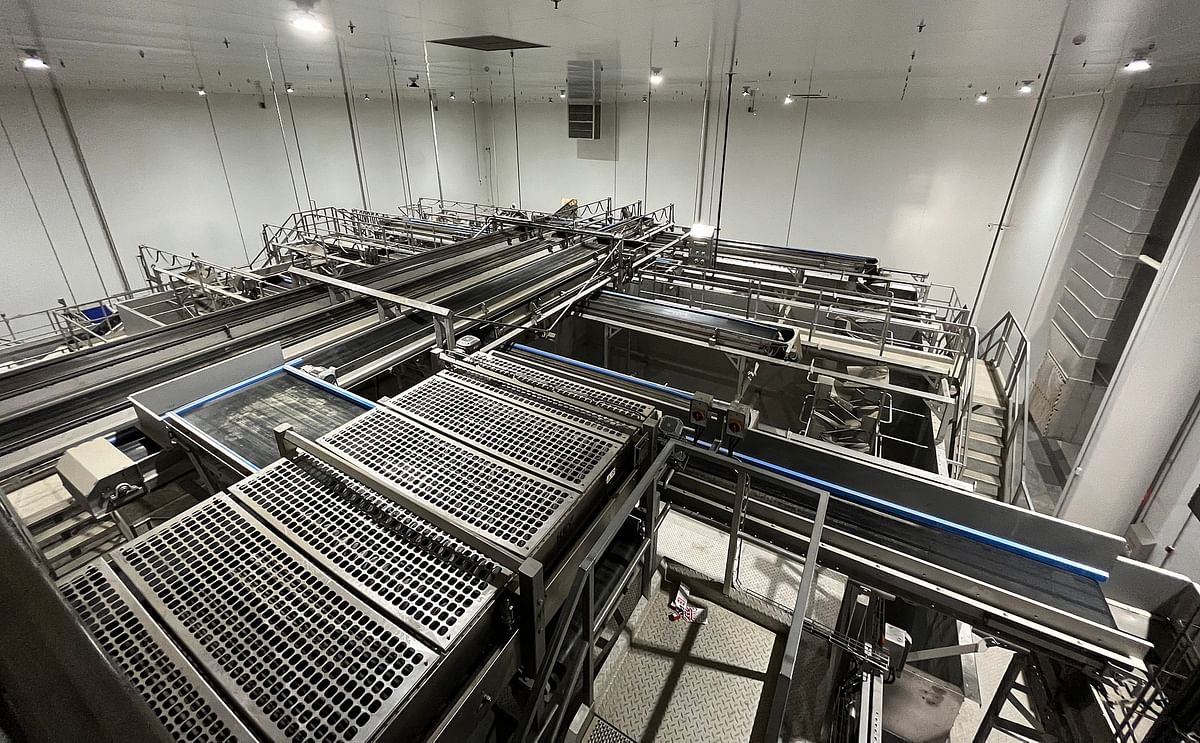
By the end of 2022, in a well-known potato growing area in China, the factory buildings were ready to be furnished with a Grisnich receiving, cleaning and sorting plant.
The delivery scope of this project consisted of as many as 37 sea containers shipped from Emmeloord to China. The plant will eventually process potatoes into french fries and potato specialities.
The Grisnich line has a receiving capacity of about 80 tonnes per hour, with potatoes being supplied from the storage area by belt trailers. The product is transported up from the chute to a sampling machine that automatically samples from the line and collects the samples in small crates. The product stream is then passed to magnets to remove any steel present.
The product then goes to the de-grounding unit. This combined unit consists of an axial cleaner, a spiral roller degrinder and a hedgehog belt with waste conveyors. The cleaning intensity is matched to the product. The waste is transported to a waste bunker outside the building.
After de-grounding, the potatoes are either first sorted or transported directly to the bunkers with a capacity of 100 tonnes. A third option is that they go directly to the washing line. Size sorting is done with two roller sorters for separating into 4 sizes.
After the roller sorter, the potatoes continue their way over two length sorters and the sorted sizes go directly into the bunkers. Each potato size can then be transported to each bunker. The undersize is transported to a separate crate.
The bunker plant consists of 8 ventilated bunkers, with a capacity of 50 tonnes each, and the bunkers are filled by bunker filling belts in combination with a drop crusher. From the bunkers, the potatoes are transported to a washing line.
This washing line consists of a stone/clod separator, drum washer and salt bath. The washing line has a capacity of about 50 tonnes per hour. After cleaning, the potatoes go directly to the even flow bunker before being transported to the process line.
The delivery scope of this project consisted of as many as 37 sea containers shipped from Emmeloord to China. The plant will eventually process potatoes into french fries and potato specialities.
The Grisnich line has a receiving capacity of about 80 tonnes per hour, with potatoes being supplied from the storage area by belt trailers. The product is transported up from the chute to a sampling machine that automatically samples from the line and collects the samples in small crates. The product stream is then passed to magnets to remove any steel present.
The product then goes to the de-grounding unit. This combined unit consists of an axial cleaner, a spiral roller degrinder and a hedgehog belt with waste conveyors. The cleaning intensity is matched to the product. The waste is transported to a waste bunker outside the building.
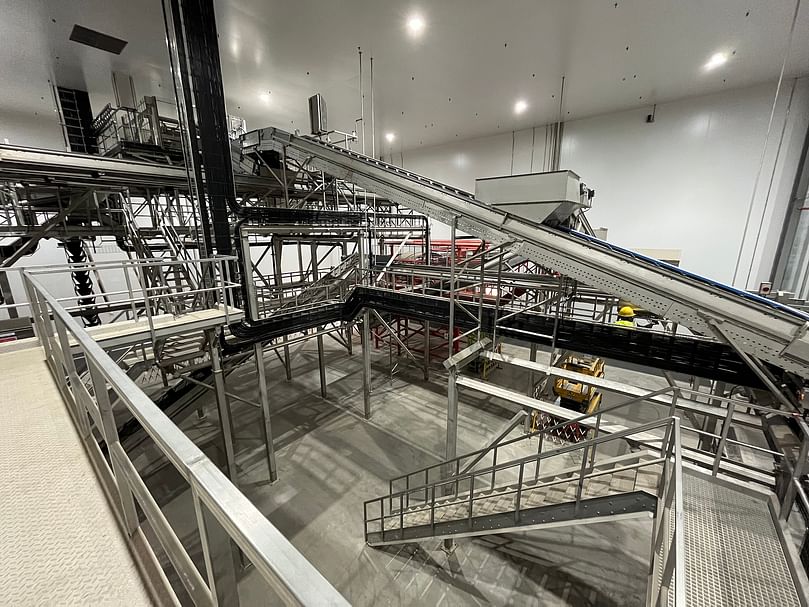
Grisnich receiving, cleaning and sorting plant in China
After the roller sorter, the potatoes continue their way over two length sorters and the sorted sizes go directly into the bunkers. Each potato size can then be transported to each bunker. The undersize is transported to a separate crate.
The bunker plant consists of 8 ventilated bunkers, with a capacity of 50 tonnes each, and the bunkers are filled by bunker filling belts in combination with a drop crusher. From the bunkers, the potatoes are transported to a washing line.
This washing line consists of a stone/clod separator, drum washer and salt bath. The washing line has a capacity of about 50 tonnes per hour. After cleaning, the potatoes go directly to the even flow bunker before being transported to the process line.
¿Te gustaría recibir noticias como esta por correo electrónico? ¡Únete y suscríbete!
Únete a nuestra Telegrama ¡Canal para actualizaciones periódicas!